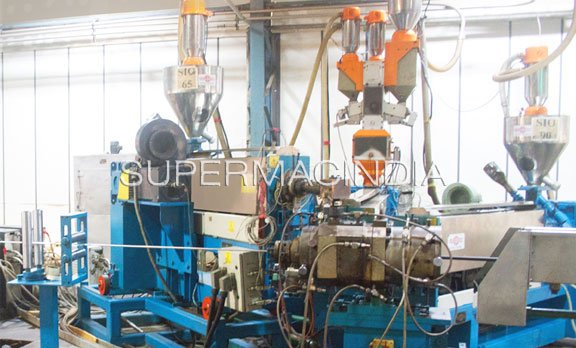
With unlimited uses for props, masks, costumes, jewelry, scenic details, these thermoplastic accouterments were developed for the medical assiduity for use in slivers and casts. The primary advantages of thermoplastics over conventional scenic molding and sculpting accouterments are quick-drying/ set-up times, lack of unhealthy or poisonous smothers or dust, and ease of use by unskilled workers. The main disadvantage is fairly high cost. But, there are no waste scraps that can be hotted and reused.
Protoplast Wastes Solid and Perforated Plastic:
When you want a nice, smooth face, and a fairly rigid structure, the solid wastes are stylish. The perforated wastes stretch better over deep relief. Stylish suited to low detail operations, structures, etc.
Protoplast Bullets:
Bullets are a better choice for thermoplastic machine manufacturer than wastes for free-form molding and are perfect for erecting up relief on the other plastics. When melted in water (in a visage used for crafts), the bullets turn veritably soft and fruity. It can be carved into low detail decorations and shapes. Will take detail when cast in molds. It can also be used as a cement to cleave other plastics to each other, support edges, etc. Vended by the pound. Thermoplastic machine manufacturer make cloth net dipped in plastic. Use the net texture to your advantage when doing dinghy, vines, etc. Can stretch about 10. When used for masks and other props, the fabric can be fused to it, or stuck to it when the plastic is hot.
The texture of a Good Thermoplastic:
The smoother plastics (Protoplast and Polyform) benefit from priming with Rosco’s Tough Florescence or other manuals for plastics.
Temperature:
Dry heat ( generally in the form of a heat gun or hair teetotaler) can also be used for the original forming or latterly to make up areas or to reshape. The material can also be carved latitude without earth. The possibilities are limited only by your imagination. Experts in W&H’s Retrofit department specialize in contemporizing being outfit, for illustration tube extrusion machine with the rearmost air ring technology. Our masterminds will be happy to help you optimize your VAREX blown film lines, cast film lines as well as extrusion outfits from other thermoplastic machine manufacturer. Increased profit and better quality at a reasonable price is a thing of every film manufacturer. Our experience is that it’s not always necessary to invest in a new line to achieve advanced affair situations. Frequently tube extrusion machine being machine is all that is demanded.
These plastics all cleave to themselves and most other accouterments readily. When forming over or into the earth, it’s stylish to apply an earth release, similar to Vaseline Intensive Care Lotion, to make it easier to remove the plastic from the earth. A tube extrusion machine involves an aged outfit that’s formerly positioned in the footmark of a client’s installation.
Johnson said some companies conclude to build blown film lines over a new line because of the capability. To use being bottom space rather than having to add on a new structure expansion. Retrofits also have a shorter design cycle time.
Conclusion:
Because thermoplastic can be recovered and reincorporated into the raw material force, you’ll nearly always see an advanced piece yield overall from your material stock than if a thermoset was chosen. Although thermoplastics are high in cost, products satisfy all the costs. Be sure to take that factor into account when probing and sourcing accouterments for your product.